Sustainable Use
As a global leader in home appliances, Whirlpool strives to minimize our environmental footprint by adopting energy-efficient technologies, enhancing repairability and recyclability and promoting a circular economy without compromising on performance, product safety, reliability and our high standards.
Scope 3 Emissions
Through assessments of our major appliances, we have learned that our largest area of impact is in the product use phase due to energy consumption (scope 3 category 11). For this reason, increasing product energy efficiency through design and engineering innovations is a top priority.
In 2024, we saw an ~2.5% reduction in greenhouse gas emissions from the use of our products as a result of product efficiency improvements and grid improvements in most sales regions. We also engaged regularly with platform stakeholders to find opportunities to meet or exceed our scope 3 category 11 emissions target, developed a cross-category energy-efficiency roadmap and invested in improvements to our emissions reporting process.
We continue to progress toward our Science-Based Targets initiative-approved target of 20% reduction in emissions resulting from the use of our products (scope 3 category 11) by 2030, compared to 2016 levels. Recent wins in this area include a growing number of ENERGY STAR-certified products in our portfolio, more cooking appliances that do not use gas and other product innovations such as SlimTech refrigeration insulation that help reduce lifetime emissions. We are continuously enhancing our emissions modeling capabilities to project business scenarios and rank contributing factors, supporting progress tracking toward our targets.
Scope 3 Category 11 Emissions
(MT CO2eq in millions)

Understanding the Life Cycle
of Our Products
We use life cycle assessments to analyze the environmental impacts of our products, often using a single product as a representative example of impacts across a particular category.
For example, we recently performed a life cycle assessment for our KitchenAid small appliance products, including the stand mixer, blender and food processor, examining materials and supplier operations, manufacturing, use, distribution and end of life.
Circular Economy
Whirlpool is committed to integrating circular economy principles into our product design, manufacturing and in the management of appliances’ end of life. We leverage our expertise as a leader in sustainable design as well as that of suppliers throughout our supply chain to design products, processes and systems that help to minimize waste, maximize resource efficiency and promote the reuse and recycling of materials throughout a product’s life cycle. We focus on embedding reliability, repairability and durability into the product development process, taking steps to engineer our products for sustainability.
Circularity is a key component of our sustainability strategy, embedded company-wide and aligned with standards such as International Organization for Standardization (ISO) 14009:2020, which helps increase circularity across the life cycle of our products. Our approach encompasses:
- Material choices to minimize the use of virgin and/or fossil-based materials
- Circular use to extend and optimize the useful lifetime of products
- End-of-life product recovery to minimize e-waste pollution and allow material recycling
Recognizing the complexity as well as opportunity embedded within the life cycle of durable consumer goods, Whirlpool Corporation established an Enterprise Circularity program at the beginning of 2024. Enterprise Circularity represents the intersection of the concepts of Using Better, Using Longer and Using Again, while also incorporating the potential for developing new sources of revenue and value recovery.
Our Circular Economy Framework
Materials Use
We select product materials with the same care and attention that our consumers use when choosing appliances for their homes and adhere to current industry compliance standards stating what is not in a component.
Restricted Materials List
We use a restricted materials list with our suppliers to help ensure that our products comply with various regulations relating to the use of chemicals, materials and other substances in our products. Our policies and materials guidance are reviewed and updated yearly to reflect new restrictions and consumer requirements. This process fosters proactive strategies that pave the way for future material innovations.
Suppliers play a pivotal role in our efforts, and we focus on equipping them with the tools and capabilities needed to increase and accelerate disclosure. We use surveys and other means to assess their performance and alignment with our standards and policies.
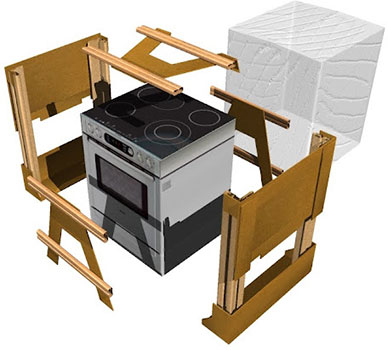
Packaging
Whirlpool seeks ways to replace non-recyclable packaging and other disposable materials with more eco-friendly solutions. We collaborate with suppliers on design enhancements and suggest alternative materials. As one example, we are actively exploring alternatives to traditional single-use plastic packaging. Through technical qualifications, we have also identified opportunities in foam and film replacements without compromising product performance. These developments are expected to help us reduce our dependence on fossil fuels, minimize scope 3 emissions and increase our use of renewable resources.
Material Recyclability
We recently successfully replaced virgin plastic materials with post-consumer resin (PCR) in our Rio Claro and Joinville plants in Brazil. A resin blend containing recycled plastic is now being used on washer tubs and refrigeration evaporation trays. In 2024, this increased the PCR content in laundry tubs to 12% and in evaporation trays to 60%, without impacting quality or performance.
Product Safety
Whirlpool has a comprehensive product safety system, encompassing the entire product life cycle and focused on identifying, evaluating and mitigating potential hazards to ensure consumer safety. Our safety system is designed to prevent issues from occurring. Therefore, we focus on training and development of our employees, the design and manufacturing of our products, and setting policies that promote proper oversight and governance of product safety. Many of our management systems are certified to industry standards.
To help equip employees across functional areas to meet expectations for product safety, we offer various training and competency programs. In our product development functions, we require each employee to achieve a targeted level of tools and methods proficiency based on their level in the organization. In our manufacturing function, Whirlpool employees are trained on the importance of process control and critical parameter management to promote the highest standards of quality and product safety.
In addition, we have procedures in place to monitor consumer complaints that could be evidence of a potential product safety risk. This allows us to quickly identify root causes of incidents, gives us the information we need to pursue corrective and preventive actions to help eliminate the possibility of recurrence and informs our decisions to pursue a recall where necessary to protect consumers. When we choose to initiate a recall, Whirlpool discloses this publicly, and we have procedures in place to manage recall operations and crisis management. There were no recalls initiated in 2024.
In 2024, 100% of new products launched to the market were evaluated in our own engineering test laboratories against internal and external product safety standards and tested and certified by a third-party laboratory. We also implemented an independent audit program for our product safety operations, which provides a “fresh eyes” review, fostering disciplined execution and identifying corrective actions where needed in the system. An audit was completed in 2024, resulting in the highest possible result, with subsequent audits scheduled for following years.
Whirlpool participates in industry technical committees to elevate external safety standards that protect consumers and advance product safety across the industry. In 2024, we had 89 employees participate in technical committees and nine employees leading with insight, data and expertise. We are taking decisive actions to sharpen our involvement and leadership in these efforts in coming years.
Product Safety Metrics
655 employees’ product safety
competency improved through
training and application
4,340+ hours of training
time completed
18 potential safety
issues resolved
0 recalls issued
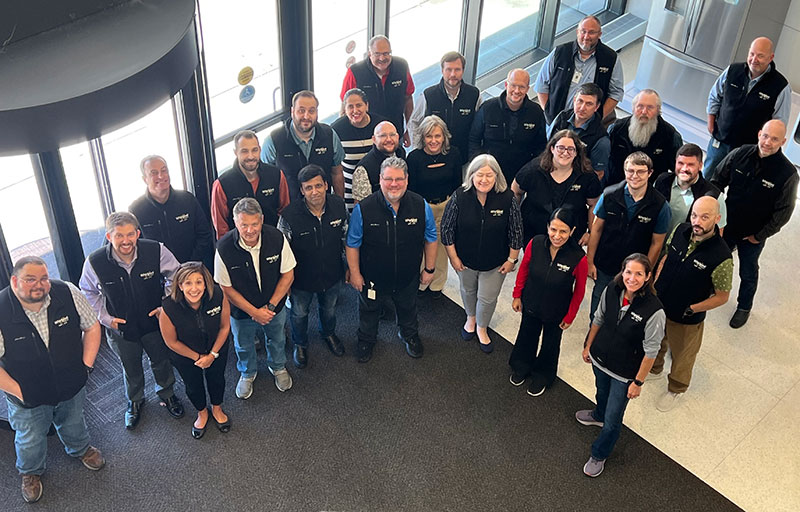
Prioritizing Reliability
We intentionally design products with reliability — and therefore safety and sustainability — in mind. To make our products more reliable and protect our consumers, we have developed accelerated lifespan and forced failure testing which allow us to anticipate issues and design appropriate solutions. We craft our products for enduring quality and support consumers with warranty programs and component accessibility.
Product Quality
Our product portfolio is at the center of everything we do, and we are passionate about our products’ quality. In 2024, we refreshed our Quality Principles and shared them across the organization. This work builds upon the new approach to our Product Leadership Scorecard, which prioritizes three important elements of consumer feedback — Quality, User Satisfaction and Value (a metric that weighs the cost of a product alongside its features, aesthetics and craftsmanship). This approach has raised the bar for the level of quality we expect to deliver to our consumers.
Designing Quality Products
To drive advancements across a broad scale, the Quality team joined a cross-functional effort to create an improved Whirlpool Product Development process. One outcome of this work was the creation of a new Project Maturity Workbook to simplify project assessments and embed our longstanding Advanced Product Quality Planning principles into a common assessment tool. We also embedded Quality roles directly into project execution teams and engineering functions.
Reacting to Quality Events
To address quality events when they do occur, we introduced several improvements in 2024, including an expanded Corrective Action/Preventive Action system across all manufacturing locations and product categories that helps us better identify and prevent issues throughout the product life cycle. In 2024, we closed issues 35% faster by implementing a new management system for improved visibility of all open issues in the system. We also introduced data analytics tools that allow us to react swiftly to quality issues in the field. With these enhanced tools and early warning detection systems, we can identify potential issues faster than ever before to protect our consumers.
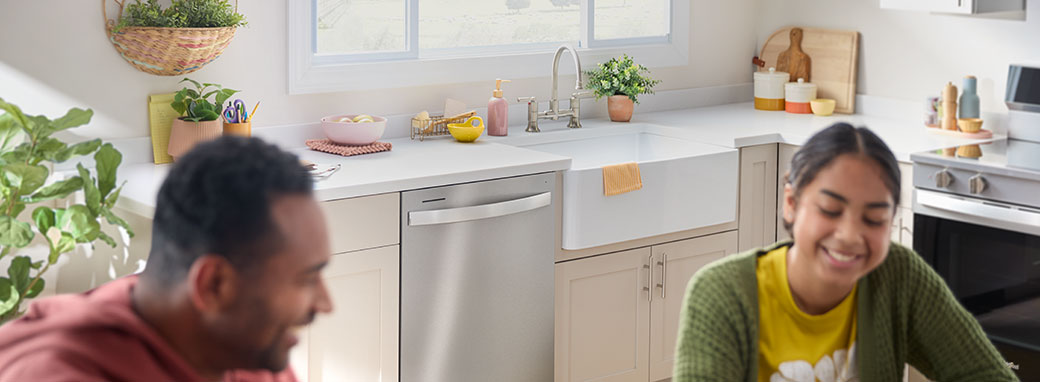
Quality Mission Statement
Together, we improve life at home by being the undisputed quality leader in appliances while delivering the best consumer experience.
Our Product Awards and Recognition
Best Top-Load Washers —
Best for Pet Owners
Architectural Digest
Maytag
Best Product Awards: Kitchen — Best Refrigerator
Best Kitchen Appliance Brands That Offer Unparalleled Performance
Forbes Vetted
Maytag
Best Wall Oven Brand
Consumer Reports
KitchenAid
Best of The Kitchen & Bath Industry Show (KBIS)
Reviewed.com
JennAir 30” Column Refrigerator with SlimTech insulation technology
KitchenAid Counter Depth 4-Door Refrigerator
Best Washing Machines —
Best for Pet Households
Tom’s Guide
Maytag
Best Electric Dryers —
Best Budget
Forbes
Whirlpool
Red Dot Award: Product Design
KitchenAid Espresso Collection
Best Refrigerators —
Best for Small Kitchens / Best Brand for Replacing Parts
CNET
Whirlpool
Best Washer and Dryer Sets —
Best for Pets
U.S. News & World Report
Maytag
Best Espresso Machines for
At-Home Baristas —
Best Fully Automatic
Best Products
KitchenAid
iF Design Award
KitchenAid Go System
KitchenAid Grain and Rice Cooker
Best of KBIS
Gold Award
JennAir 30” Column Refrigerator with SlimTech insulation technology
Repairability and Refurbishment
To make our products more repairable, we make components accessible and easy to disassemble and offer spare parts for at least seven years in our North America region and 10 years in Europe and LAR. Our cross-functional team is working to make access to documentation, tools, diagnostics, service parts and firmware available to anyone who wants to repair and lengthen the lifespan of our products, adding to our already robust library of repair manuals.
Occasionally, products may be damaged, returned or discarded early in their lifespan. In these cases, they often can be restored to like-new condition at one of our refurbishment centers. There, they undergo a comprehensive inspection, are repaired if needed, tested and resold or sometimes donated to nonprofits through programs like our Feel Good Fridge program in the U.S. and disaster relief organizations. Whirlpool operates refurbishment centers in North America, South America and Europe. We operate these centers both independently and in collaboration with logistics centers, where we also repair and refurbish products.

Global refurbishment centers results in 2024:
618,925 total returned
products
390,076 total refurbished
products
63% returned products
refurbished
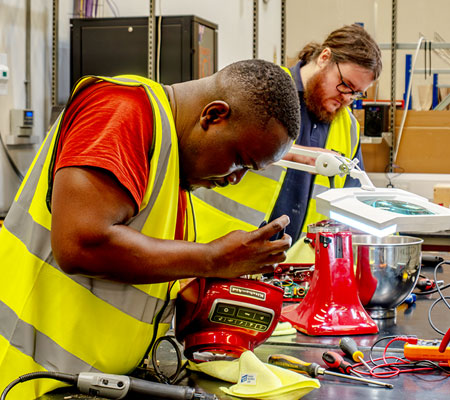
Promoting Repair and Refurbishment in the United States
Our KitchenAid Small Appliance Operations in Greenville, Ohio, inspects, repairs and refurbishes small appliance returns from the U.S. and Canada. In 2024, the team added seven new categories of products to their refurbishment process and refurbished more than 95,000 products, representing 43% of the returned product received. Many of the refurbished products are re-sold through internal sales with proceeds being donated to United Way.
End-of-Life Management
End-of-life products are disposed of in line with Waste of Electrical and Electronic Equipment regulations. For countries with an Extended Producer Responsibility (EPR) policy in place, we work through producer responsibility organizations to comply with regional targets. For countries without an EPR policy, we aim to promote responsible collection and treatment of disposed appliances either directly or indirectly.
To manage compliance and improve oversight of our waste management processes, we developed and implemented a Recycling Service Agreement with our vendors. This agreement requires they comply with local laws and regulations for proper waste management and provides procedural guidelines to help ensure that any hazardous components (as defined by laws and regulations) are properly identified and processed in the end-of-life phase. We also require suppliers and subcontractors to follow the Basel Convention regarding the ban or exportation of e-waste from Organisation for Economic Co-operation and Development (OECD) countries to non-OECD countries.
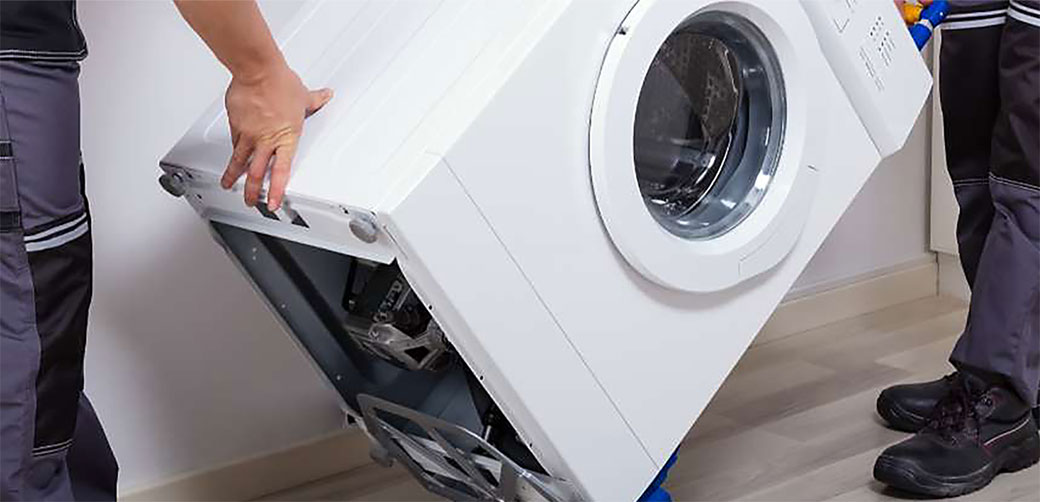
Addressing Electronic Waste in Brazil
In Brazil, Whirlpool is the first appliance company to offer free home collection nationwide for electronic equipment waste of any brand weighing more than 30 kilograms, including refrigerators, washing machines, dryers and ranges, through our Take Back System.
Consumers can also take small electronics and appliances to more than 15,000 collection points across 5,558 municipalities, throughout the country, free of charge. Whirlpool works with Circulare, a platform that connects a circular economy ecosystem focused on electronic waste management. Our Take Back System helps address the challenge of 2.4 million tons of electronic waste generated annually in the country,2 fostering materials recycling and avoiding environmental impacts.
55,000+ tons electronic waste treated through Whirlpool Corporation’s Take Back System (Sept. 2023–Dec. 2024)
15,000+ collection points nationwide
100% of Brazil's territory municipalities with free home collection
- 2024 scope 3 category 11 emissions data is inclusive of the divested EMEA business through the transaction closing date. In 2025, we will be reevaluating the baseline and boundaries associated with our scope 3 category 11 emissions target in response to changes in Whirlpool Corporation’s organizational structure.
- Source: 2024 E-waste monitor. United Nations Institute for Training and Research, November, 2024.