Occupational Health and Safety
Every Whirlpool employee, everywhere, shares the responsibility for protecting their own safety, as well as the safety of their colleagues, contractors and other visitors.
The health and safety of our people, including visitors and contractors, is critical to the operation of our company. Our We Care EHSS Management System guides our risk-reduction efforts. Each manufacturing location self-assesses against these standards annually, and an on-site corporate governance assessment validates the results every third year.
Our Policies to Encourage Safe Practices
See our EHSS Policy for details on how we are keeping our employees and contractors safe.
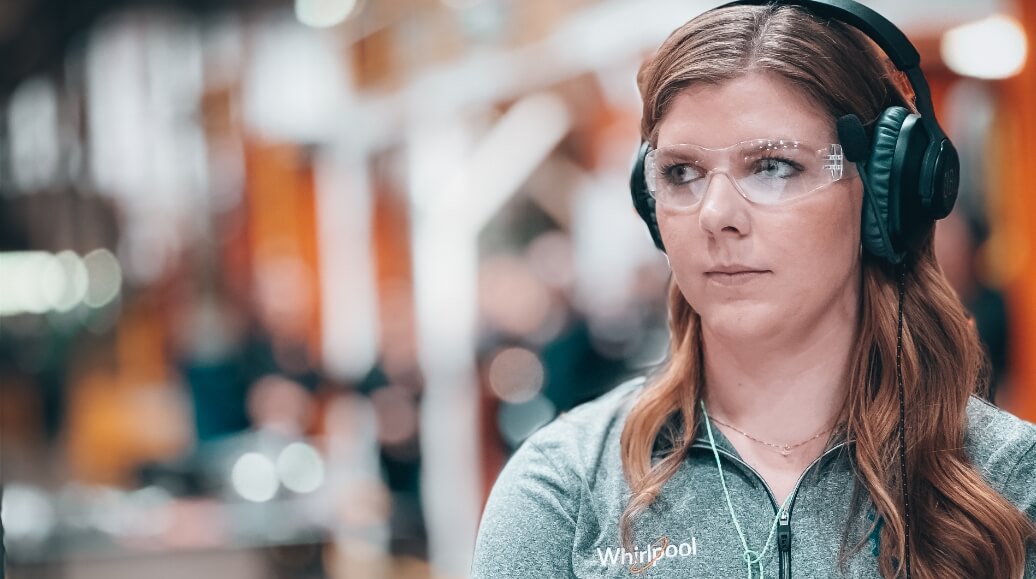
Safeguarding Our Employees:
Our Attitudes for Life
Whirlpool workers in our manufacturing, warehouse and field service locations sometimes have to engage with processes, machinery and equipment that present safety hazards. We manage these hazards and reduce risk by using carefully designed controls and systems, layering multiple defenses and requiring competent, authorized workers. Our Attitudes for Life are foundational precautions and desired behaviors aimed at preventing serious and life-altering injuries to our employees and contractors performing high-risk activities.
We raise awareness and train employees at all our facilities on our Attitudes for Life, while also training them to intervene when co-workers face a potentially high-risk situation. We encourage employees to speak up when safety questions or concerns arise. If preferred, employees can report confidentially through the Whirlpool Corporation Integrity Line.
Our Attitudes for Life Are a Shared Responsibility
We maintain and display safety information and reinforce the procedures to keep employees safe, no matter what type of hazardous activity they encounter, including:
- Confined Space Entry
- Hazardous Substances
- Driver Safety
- Electrical Safety
- Crane, Hoist and Lifting Equipment
- Powered Industrial Vehicles
- Machine Safety
- Hazardous Energy Control
- Work at Height
- Hot Work
Safety Focus Site Program
Recognizing that some operations require more support than others, Whirlpool introduced the Safety Focus Site program in 2023. The program is designed to increase visibility of safety risks at these sites to leadership and to place regular, focused attention on activities that should improve safety performance. Site leaders report their performance to regional and corporate leadership at least monthly to obtain direction and feedback and drive accountability. Since the program began, there has been an overall decrease in the number of injuries sustained by Whirlpool employees.
In 2024, seven sites were selected based upon opportunities to improve injury-prevention performance. Given the positive results, the Safety Focus Site program will continue into 2025 and expand to additional sites.
Safety Focus Site Program Increased Employee Safety
38% reduction in recordable
injuries and illness
36% reduction in recordable
injury and illness rate
21% reduction in lost time
injuries and illness
18% reduction in lost
workday rate
Prioritizing Contractor Safety
Whirlpool takes contractor safety seriously. We expect the same proactive and preventive mindset among contractors as we have among our employees. All potential contractors that conduct high-risk activities must pre-qualify to work with Whirlpool by demonstrating environment, health and safety compliance and a history of positive performance. We extend our expectations for our Attitudes for Life to our high-risk contractors, including consequences of non-compliance, which can include disqualification from working at any Whirlpool location.
Safety Performance
Whirlpool tracks industry standard health and safety key performance indicators, including total recordable incident rate, lost time incident rate and serious incidents.
Over the past five years, Whirlpool has shown a consistent decline in incidents. In 2024, we reduced serious injuries by 50%, our recordable injury and illness rate by 12% and our lost workday rate by 16% compared to 2023. In addition, we compare our incident performance against the industry through the U.S. Bureau of Labor Statistics North American Industrial Classification System data for the Major Household Appliance Manufacturing Industry, and we have consistently and strongly outperformed the industry’s average.
See our Data Appendix for additional metrics.
Whirlpool Injury Rates Versus Industry: Four-Year Trend
Recordable Injury & Illness Rate1
- Whirlpool
- Industry Average 20234
Lost Workday Rate3
- Whirlpool
- Industry Average 20234
- Whirlpool
- Industry Average 20234
340% better than the industry average
133% better than the industry average
- Recordable injury and illness rate is calculated as number of recordable injury and illness cases multiplied by 200,000 (100 full-time-equivalent employees/non-employees working 40 hours per week for 50 weeks) then divided by the number of hours worked for the reporting period.
- 2024 data is inclusive of the divested EMEA business through the transaction closing date.
- Lost workday rate is calculated as number of the days away from work cases multiplied by 200,000 (100 full-time-equivalent employees/non-employees working 40 hours per week for 50 weeks) then divided by the number of hours worked for the reporting period.
- Bureau of Labor Statistics. "Table 1-Incidence Rates-Detailed Industry Level.” NAICS 33522 (Major Household Appliance Manufacturing).