OUR PLANTS AND OPERATIONS
Driven by innovative, modern technology and individuals who look after the safety and well-being of one another, Whirlpool Corporation facilities aim to be the benchmark for global manufacturing excellence.
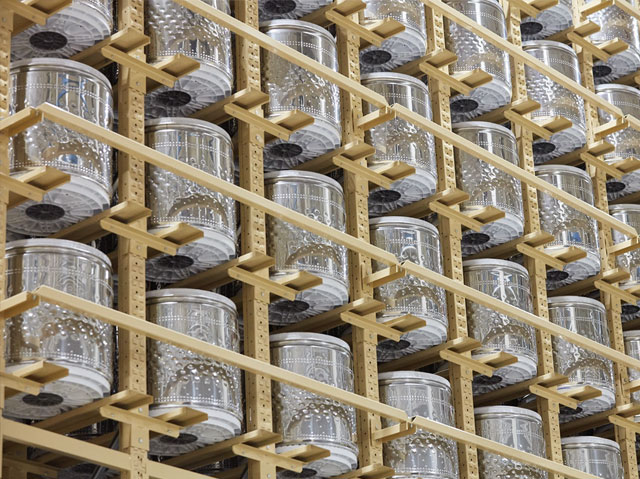
Sustainable Operations
Through strategic investments and strong facilities management systems, we continue to make our manufacturing and distribution network stronger, delivering best-in-class, global operational excellence.
Whirlpool Corporation's facilities operate under our “We Care” Environment, Health, Safety & Sustainable Operations (EHSS) Management System, an operating framework which is aligned to International Organization for Standardization (ISO) 14001:2015 and 45001:2018. We Care outlines four commitments for employees at all our workplaces:
- Protect our people
- Preserve the environment
- Enable the business and our people to act sustainably
- Share the responsibility
Our use of World Class Manufacturing (WCM) methodology helps to improve productivity and quality while reducing losses in production systems. Further, WCM promotes responsible resource use throughout our facilities. We also use real-time data and analytics, artificial intelligence and equipment connectivity to maintain a best-in-class manufacturing and distribution network that reduces energy consumption, resource use and carbon emissions.
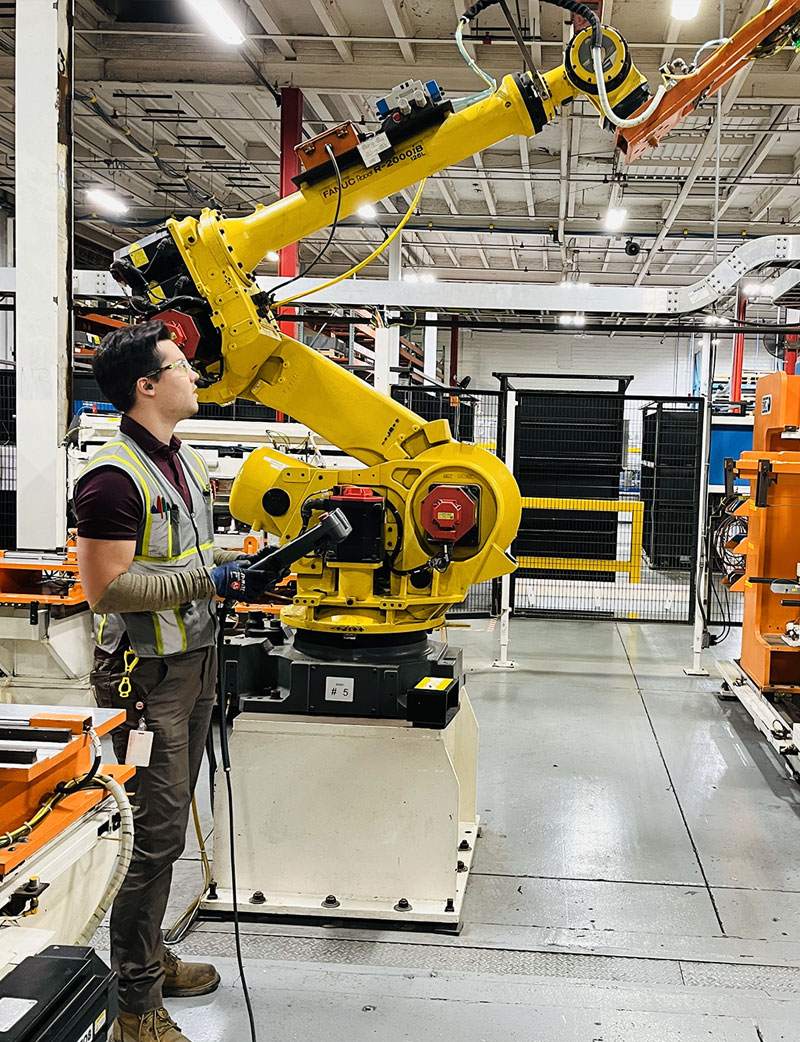
World Class Manufacturing
-
Safety
-
Cost Deployment
-
Focused Improvement
-
Autonomous Maintenance
-
Workplace Organization
-
Professional Maintenance
-
Quality Control
-
Logistics and Customer Service
-
Early Equipment Management
-
People Development
-
Environment and energy
Energy and Emissions
Energy and emissions reductions are fundamental to a WCM operation and the centerpiece of our environmental footprint management. In 2003, Whirlpool Corporation was the first appliance manufacturer to set an emissions reduction target. In 2021, we announced our global commitment to reach Net Zero emissions, scopes 1 and 2, in our plants and operations by 2030, and have continued to make significant progress in emissions reductions each year.
Our innovative manufacturing processes require a lot of energy. As a key driver of greenhouse gas (GHG) emissions reduction, energy management is a priority within our four-point plan to achieve our Net Zero emissions target.
Our Four-Point Plan to Reduce GHG Emissions
Reduce Energy Usage
Reduce energy consumption through both WCM efficiency projects and facility retrofits. Projects include LED lighting, compressed air use reductions, and boiler and HVAC optimization.
Expand Renewables
Implement 100% renewable energy for electricity consumption.
Electrify/Substitute
Electrify and substitute fossil fuels (with hydrogen, bio-gas or other) everywhere possible to reduce scope 1 emissions.
Carbon Offset Credits
If necessary, invest in high-quality carbon removal projects and any other carbon credits to offset unavoidable emissions.
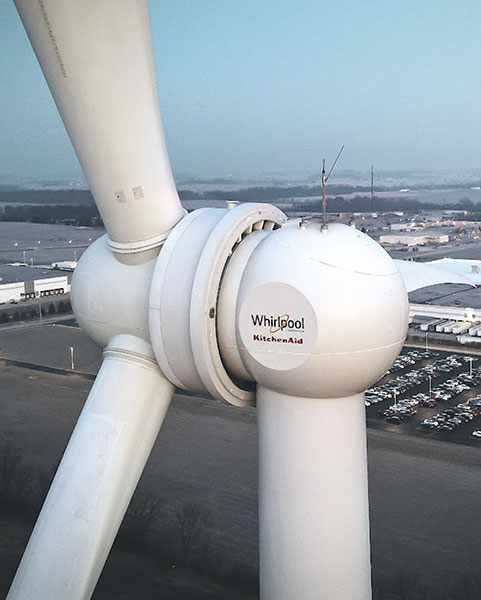
Progress Toward Our Goals
In 2024, we reduced scopes 1 and 2 emissions by 36%1 compared to 2023, keeping us on track to achieve our 2030 goal. This is the third year in a row that we have achieved double-digit reduction. Reducing energy usage has been a key driver for these results, with the Energy pillar in WCM guiding our efforts to lower energy costs and improve energy efficiency. In 2024, including the Europe, Middle East and Africa (EMEA)2 region which we divested in early Q2, we fell short of our energy intensity target of 3% reduction for the year. For operations in North America Region, Latin America Region, and India, we achieved an 8% year-over-year reduction in energy intensity in 2024.
In the United States, we had a significant milestone in 2024 in our path to Net Zero. Whirlpool has achieved our goal to reduce 50% of the GHG emissions in our U.S. manufacturing sites from the 2019 base year, in support of the U.S. Department of Energy (DOE) Better Climate Challenge.
Driving to Net Zero Emissions in Our Plants and Operations (MT CO2eq)
Market-Based Emissions
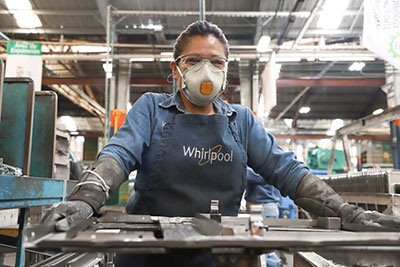
High-Impact Energy Efficiency and Decarbonization Projects Implemented in 2024
Celaya, Guanajuato site, Mexico: The pre-paint cleaning process electrification is a great example of one of our main paths to decarbonization of our plants through substitution of fossil fuels. The Celaya Energy pillar team replaced the use of steam from a central boiler with localized electric heaters, with a goal to eliminate natural gas and reduce around 700 metric tons (MT) of carbon dioxide equivalent (CO2eq) emissions, contributing to approximately 5% reduction in their total scope 1 emissions.
Findlay, Ohio site, United States: The Findlay site implemented a regenerative thermal oxidizer pollution abatement system, replacing a direct-fired natural gas system with a more energy-efficient solution. The new system uses ceramic media to capture and reuse waste heat, enabling the efficient and effective destruction of volatile organic compound emissions from a paint operation. This project will significantly reduce natural gas consumption and avoid approximately 1,500 MT of CO2eq emissions, contributing to a roughly 14% reduction of the site’s scope 1 emissions.
Supsa site, Nuevo León, Mexico: The site purchased an advanced burner control system for the polymerization oven to improve efficiency and decrease natural gas use. This change will reduce CO2eq emissions from refrigerator door paint-curing ovens and will reduce approximately 625 MT of CO2eq emissions at the site, contributing to approximately 19% reduction in their total scope 1 emissions.
Operational Innovations to Reduce GHG Emissions
We are continuing to work with Centrepolis Accelerator at Lawrence Technological University in Southfield, Michigan, to research opportunities for sustainability innovations for our operations.
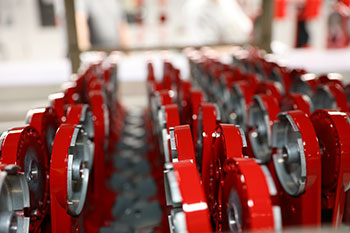
In October, the U.S. DOE Industrial Efficiency and Decarbonization Office awarded $1.2 million in federal funding to advance efforts to improve energy efficiency in industrial coatings led by Centrepolis Accelerator. The project will validate and pilot a lower-energy, laser-based powder coat curing technology for decarbonizing industrial coating operations with Whirlpool as a key industry advisor, as well as IPG Photonics and PPG Industries. This advanced technology is designed to replace traditional natural gas curing ovens, offering a more energy-efficient, electrically powered alternative that reduces on-site GHG emissions.
The project aligns with the DOE’s Industrial Heat Shot™ initiative, which aims to develop cost-competitive technologies to decarbonize industrial heat by reducing GHG emissions by at least 85% by 2035.
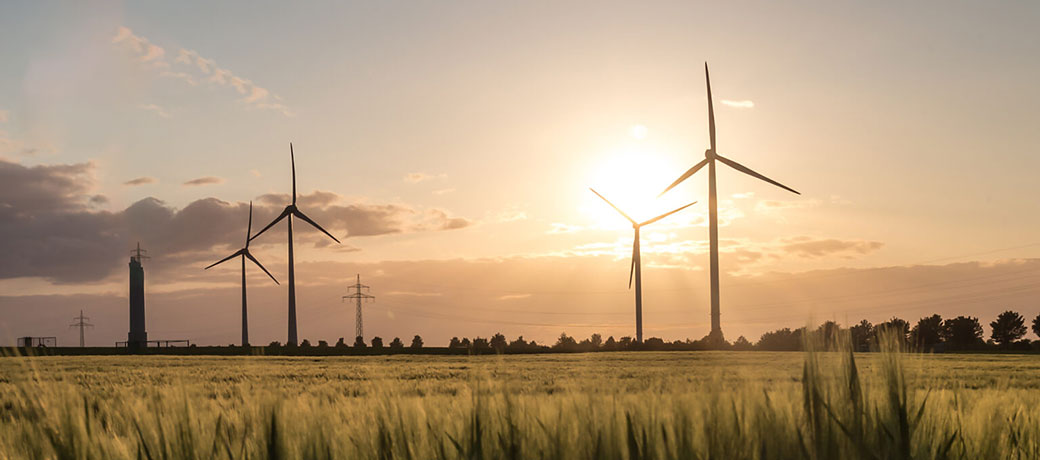
Whirlpool Recognized as a Top Green Energy Investor in the U.S.
Whirlpool Corporation's investment in renewable energy has been recognized by the U.S. Environmental Protection Agency (EPA) as being among the highest in the country. In 2024, we ranked 60th in the EPA’s National Top 100 List of the largest green power users from the Green Power Partnership, 14th on the Top 30 On-site Generation list and 34th on the list of Green Power Partners from the Fortune 500®. According to the EPA, we purchase more than 301 million kilowatt-hours of energy from renewable sources annually in the U.S.,3 representing 86% of our manufacturing operations’ total power needs.
We joined the EPA’s Green Power Partnership in 2019 by declaring our voluntary investment in green power to protect human health and the environment.
Renewables
Second only to the reduction of energy use overall, replacing fossil fuel-powered electric energy with renewables is a priority for Whirlpool. We have invested heavily in the development of on-site renewables — primarily wind and solar — at our operations around the world. These investments are supplemented by off-site renewable energy purchases.
In 2024, for the first time, we are matching 100% of our electric energy consumption not generated from on-site systems in the U.S. manufacturing sites with support from two off-site renewable energy projects: the Engie Limestone Wind farm in Dawson, Texas, and Mesquite Sky in Callahan County, Texas.
United States
In 2025, Whirlpool aims to have on-site renewables at all small appliance, dryer, washer and dishwasher manufacturing plants in the U.S. Currently, we have operational installations at four facilities, with one in development and multiple projects in the investigation stage.
SITE | RENEWABLE TYPE | STATUS | INSTALLED CAPACITY |
---|---|---|---|
SITE
|
RENEWABLE TYPE
Wind
|
STATUSOperational | INSTALLED CAPACITY30% of site’s electrical power needs |
SITE
|
RENEWABLE TYPE
Wind
|
STATUSOperational | INSTALLED CAPACITY>70% of site’s electrical power needs |
SITE
|
RENEWABLE TYPE
Wind/solar
|
STATUSOperational Additional capacity expected to be operational in early 2025 |
INSTALLED CAPACITY13% of site's electrical power needs Expected to increase to >85% |
SITE
|
RENEWABLE TYPE
Wind/solar
|
STATUSOperational Potential project for additional capacity in the planning stage |
INSTALLED CAPACITY19% of site’s electrical power needs Potential to increase to >70% |
SITE
|
RENEWABLE TYPE
Wind/solar
|
STATUSUnder construction Expected to be operational in 2025 |
INSTALLED CAPACITY70% of site’s electrical power needs (expected) |
Brazil
In Brazil, for the first year, we matched 100% of our electricity consumption in our manufacturing operations and regional headquarters with renewable energy credits (RECs). In addition to RECs, we have a small solar farm at our Joinville location in Brazil.
India
On-site renewable energy in our India manufacturing plant covered approximately 18% of our total energy consumption in the country in 2024. This includes three solar rooftop installations, one in each manufacturing site, which combine to 9 megawatts (MW) of total energy capacity, including a recent addition of 0.5 MW capacity to the Puducherry site. We plan to continue this expansion of on-site renewables.
Mexico
In 2024, we increased our purchase of RECs to match approximately 50% of electricity consumption across our sites in Mexico.
Resource Management
Although GHG emissions and energy management are the most material environmental impacts across our operations, we are also working to improve our water and waste management and support for biodiversity. Whirlpool Corporation's We Care EHSS Management System provides a common framework for our plant teams to help them manage resources around each facility and to reduce our environmental footprint.
Water
Water is a critical resource that we rely on to produce our products. We maintain high standards which, in many locations, exceed regulatory expectations. Our site in Findlay, Ohio, for example, has installed new real-time metering technology with 12 meters at machine level, through which the site was able to identify more than 7 million gallons of water loss.
Whirlpool is also a signatory to the CEO Water Mandate, a commitment to water stewardship under the United Nations Global Compact. By being an endorsing company, we committed to action across six key areas, including direct operations. Over the past few years, we have worked to improve the efficiency of our operations by reducing water intensity (water withdrawal by products produced). In 2024, we achieved our goal of 3% reduction in water intensity.
Water risk assessments are conducted regionally with use of the World Resources Institute’s Aqueduct tool to look at current and future water risks. Some of our global operations are located in areas of water stress, and in these sites, reducing water consumption is a bigger priority. Two examples include our Celaya site in Mexico and our Puducherry site in India. Celaya used an electrification project to eliminate one boiler, which helped the site reduce water intensity by 14% in 2024, while the Puducherry site installed a recirculation unit at the research and development center to recirculate water used in washing machine testing, which contributed to a 25% reduction in water intensity in 2024.
Wastewater Treatment and Reuse
Whirlpool acknowledges the potential adverse impact of wastewater and potential pollutants on water ecosystems. We track the use of hazardous chemical substances and reduce or phase them out where possible, through a chemical prioritization methodology pursued by the Environmental pillar within WCM. We also work to continually improve our processes and equipment through new technologies. For example, over the past few years, Whirlpool has developed robust coating systems for metal corrosion protection that use nanoceramic conversion instead of phosphating, the former being less chemical- and water-intensive.
We treat all industrial and sanitary discharges from manufacturing facilities either on site or externally, depending on the facility and local legal requirements. At some sites, we’ve made additional investments in water treatment technology so that we can reuse water on site. For example, in Rio Claro, Brazil, all the effluent from the technology center is treated at the internal wastewater treatment plant, which was designed to allow for 100% internal reuse of the volume treated. Our Pune and Puducherry sites in India reuse 100% of the industrial and sanitary wastewater treated on site for gardening and in toilets. Our Celaya site in Mexico reuses 100% of the sanitary wastewater treated on site for gardening.
Waste
Our Zero Waste to Landfill (ZWtL) approach to waste management, in alignment with our We Care Management System, represents a best-in-class approach to diverting waste away from permanent landfill. We invest in plant efficiency, waste reduction, recycling and other efforts to reduce waste and contribute to a circular economy.
~32,000 tons of waste diverted from permanent landfills through ZWtL program since 2016
In 2024, we achieved a 97% or higher landfill diversion rate in all our global manufacturing sites, including significant improvements made to our Fatima, Argentina, site and our Racine, Wisconsin, InSinkErator site. Both sites had achieved a 95% diversion rate in 2023, and in 2024, two years after integration into the corporation’s portfolio, the Argentina site moved to 99% diversion rate and Racine to 97% diversion rate. To achieve these results, both sites worked, among other initiatives, on improving waste segregation at the shop floor. The Racine site worked to improve their recycling rate of heavier plastic and shrink wrap, and the site in Argentina worked to improve their recycling rate of packaging waste.
Hazardous Waste
Whirlpool first set a goal to reduce hazardous waste generation in 2022, and since then our performance (hazardous waste intensity per product produced) has improved by over 25%. To achieve these results, Whirlpool has worked with a few focus sites in Brazil and Mexico, where hazardous waste generation is higher in comparison to other sites, due to differences in waste regulations. Projects included internal reuse of chemicals, on-site treatment of oily water, improved segregation of contaminated and non-contaminated personal protective equipment and recharacterization of waste streams in alignment with environmental agencies.
Biodiversity and Employee Engagement
As a global company, Whirlpool Corporation has operations in many types of ecosystems. We are committed to protecting these life-sustaining resources for future generations. Some site-specific programs include:
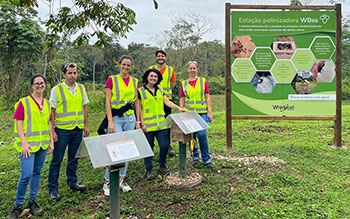
“Sustainable Pathway” program in Joinville, Brazil:
Our Joinville site boasts 174,522 square meters of protected green area. The site developed a path where people can walk and learn more about the local fauna and flora through visual information boards. Along the path, the site also implemented the WBee project, a dedicated area to preserve local species of stingless bees and support pollination of local flora. In 2024, more than 1,700 people, including Whirlpool employees, students and local authorities, had the chance to visit and learn.
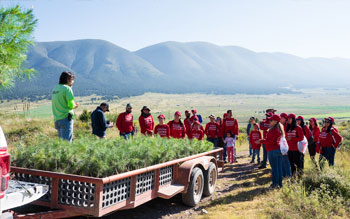
Reforestation in the mountains of Coahuila, Mexico:
In 2024, more than 100 volunteers, including Whirlpool employees and their family members, planted 850+ trees in a region that has suffered severe forest fires in recent years, affecting biodiversity, water quality and air quality. Since 2017, nearly 5,150 trees have been planted in the region.
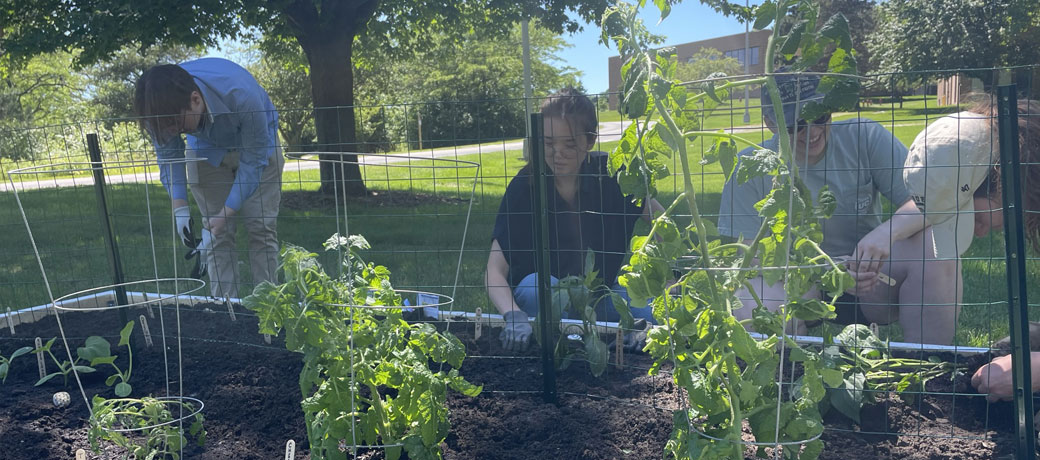
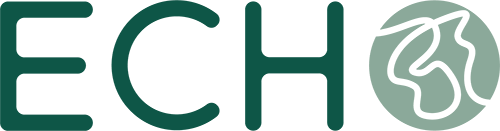
Employees are Eco-Conscious in the
Home and Office (ECHO)
In 2024, members of ECHO, an employee environmental group, championed sustainability initiatives across multiple locations. At the Benton Harbor, Michigan, headquarters, ECHO members focused on supporting local ecosystems and reducing waste. They maintained a monarch butterfly waystation to aid in butterfly migration and established a thriving vegetable garden that provided over 300 vegetables donated to employees. The team also demonstrated their commitment to the community by cleaning up over 950 pounds of trash from local parks, beaches and roads.
To minimize environmental impact within the workplace, ECHO, working with cafeteria management, successfully transitioned some cafeteria meals to compostable containers, achieving a 35% reduction in plastic waste. At the InSinkErator headquarters in Wisconsin, ECHO implemented a plastic and snack wrapper collection and recycling program in collaboration with TerraCycle.
Expanding its reach beyond the United States, ECHO launched new chapters in Brazil and Mexico, further solidifying its commitment to global environmental responsibility and empowering employees worldwide to become active changemakers.
- The 36% reduction includes 18% from the divestiture of the EMEA region and 18% from focused projects.
- On April 1, 2024, Whirlpool Corporation completed its transaction to divest the EMEA major domestic appliance business. 2024 scope 1 and 2 emissions data is inclusive of the EMEA business through the transaction closing date. In 2025, we will be reevaluating the baseline and boundaries associated with our Net Zero emissions target in response to changes in Whirlpool Corporation’s organizational structure.
- Source: Whirlpool Corporation’s Strategy for Renewable Energy in Its North America Operation Puts Company on EPA Green Power List Recognized for Green Power Leadership. Whirlpool Press Release, May 2024.